A recent study published in ACS Central Science, a journal of the American Chemical Society, suggests that cyanide, a highly toxic substance, may be linked to the origin of life. New evidence provided by Kumar Vanka and colleagues from India indicates that the origin of life could be associated with water and hydrogen cyanide (HCN). Previously, the famous Urey-Miller experiment pointed out that HCN existed on Earth before the origin of life. Other experiments have also shown that HCN may have provided the fundamental synthetic materials for the formation of RNA and protein precursors. Kumar Vanka’s work attempts to address these questions from a different perspective. They used the AINR (ab initio nanoreactor) method for molecular dynamics simulations to explain the process by which HCN and water, as raw materials, generate basic organic compounds such as glycine, cyanamide, and glycoaldehyde.
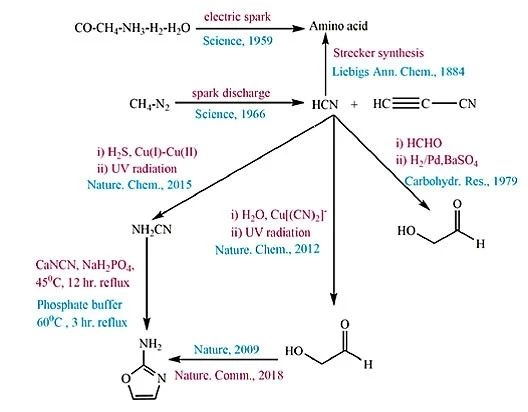
Figure 1 Process of Synthesizing Organic Compounds Using HCN as Raw Material
This study has refreshed our understanding of hydrogen cyanide, a key raw material in the chemical industry. The global hydrogen cyanide (HCN) market is approximately 17 billion RMB, with a total production capacity of about 2.7 million tons per year. As the Chinese market rapidly develops, hydrogen cyanide production capacity continues to expand. Due to its hazardous nature, hydrogen cyanide is not traded directly in the market but is typically converted on-site into the required downstream products instead of being transported. Hydrogen cyanide is also subject to various legal regulations, such as the "War Weapons Control Act."
Hydrogen cyanide, as a key raw material, is currently used in the production processes of many important products:
Diene/Nitrile
Hexamethylenediamine/nitrile is an important monomer for new materials, used in the production of nylon 66, which is a key lightweight material for automobiles. Isophorone diamine is used as a curing agent for wind energy materials and is widely employed in the new energy industry.
Chelating Agents
Important applications include pulp and paper processing; industrial water treatment; household, institutional, and industrial cleaning compounds. Chelating agents are also used in metal surface treatment, agriculture, photography, rubber processing, food, pharmaceuticals, and textile treatment.
Cyanogen Chloride
Cyanogen chloride is primarily used as a pesticide in the agricultural industry. It is also used in the production of chlorosulfonyl isocyanate, a key raw material for the lithium-ion battery additive lithium bis(fluorosulfonyl)imide (LIFSI).
Glyphosate
Glyphosate, a non-selective herbicide, is used to eliminate weeds in preparation for agricultural production. This preparation helps increase yield and generate economic value.
Amino Acids
Amino acids enable the effective production of essential proteins, making a significant contribution to providing high-quality protein for the growing global population.
Sodium Cyanide
Metallurgy is the primary application of sodium cyanide. It is also used in the production of key Prussian blue or Prussian white materials for the cathode of sodium-ion batteries.
Global Hydrogen Cyanide Production Routes
From the raw material routes, they include:
1. Natural Gas/Methane Ammonia Oxidation Method: This includes the Anden process, Degussa BMA method, and DuPont's methane pure oxygen ammonia oxidation method.
2. Light Oil Cracking Method: Developed domestically, this method uses light oil, liquid ammonia, and caustic soda as primary raw materials, with petroleum coke and nitrogen as auxiliary materials. It is mainly applied in sodium cyanide production enterprises.
3. Methanol Ammonia Oxidation Method: Originating from Asahi Kasei, this method uses methanol, ammonia, and air to react under an iron-molybdenum catalyst.
4. Shawinigan Process: This method uses ammonia and hydrocarbons (usually propane or butane) as raw materials, reacting under electric heating and fluidized bed conditions to produce hydrogen cyanide.
The natural gas route has a stable and low-cost raw material source with relatively low carbon emissions, aligning with the development trend of the chemical industry under the dual-carbon background. Today, almost all new hydrogen cyanide plants worldwide are based on the Anden process, which is the dominant technology globally, accounting for more than 50% of the global hydrogen cyanide production capacity.
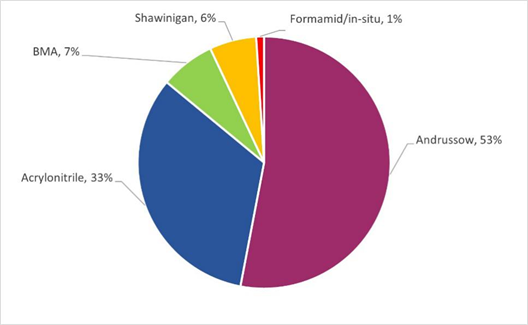
Figure 2: Market Share of Different Hydrogen Cyanide Production Technologies Worldwide
Anden Process Hydrogen Cyanide Production Overview
The Anden process uses methane/natural gas, ammonia, and air, which are pre-pressurized and mixed. The mixture is then reacted at 1100°C under several layers of platinum-rhodium alloy mesh catalysts. The reaction product contains about 5-8% hydrogen cyanide. This material is rapidly cooled below 300°C by a waste heat boiler, and then undergoes further treatment or recovery of other by-products from the reactor. The hydrogen cyanide is purified and refined to the required purity for downstream production (typically based on water content, with the hydrogen cyanide's water content ranging from 300 to 5000 ppm, depending on the downstream product).
Due to the low reaction efficiency, low conversion rates, high impurity content, low product yield, complex production operations, and difficult control associated with traditional hydrogen cyanide and its derivatives production equipment, DODGEN Company has optimized and enhanced the process in the areas of reaction, ammonia removal, and production based on its proprietary process technology. This has led to the development of DODGEN's unique hydrogen cyanide synthesis technology, making it an industry leader in this field.
DODGEN, based on the preliminary design goals provided by the customer, combines years of advanced experience and multiple plant operation experiences to simulate, estimate, and optimize the process system design. The design of the entire plant's process system has the following key characteristics:
◆ High-efficiency reaction equipment, fast gas flow rate, and high mass transfer efficiency;
◆ High equipment heat transfer efficiency, with a small temperature gradient in the reaction system;
◆ Small concentration gradient of reactants, resulting in high reaction efficiency;
◆ High reactant conversion rate;
◆ High product yield;
◆ Low impurity content;
◆ Wide elasticity range for production capacity;
◆ Good equipment start-up cycle;
◆ Continuous operation for both feeding and product extraction, ensuring good plant continuity.
The three raw materials are mixed using DODGEN's specially designed gas static mixer, which solves the technical challenge of achieving uniform mixing of large-volume raw materials, ensuring a high ammonia conversion rate for HCN. Long-term large-scale operation results have shown that by adopting DODGEN's efficient hydrogen cyanide synthesis technology, combined with DODGEN's self-developed fast and medium-speed reaction equipment for hydrogen cyanide and its derivatives, there has been a significant improvement in reaction efficiency, conversion rate, and product yield, while effectively controlling impurity content.
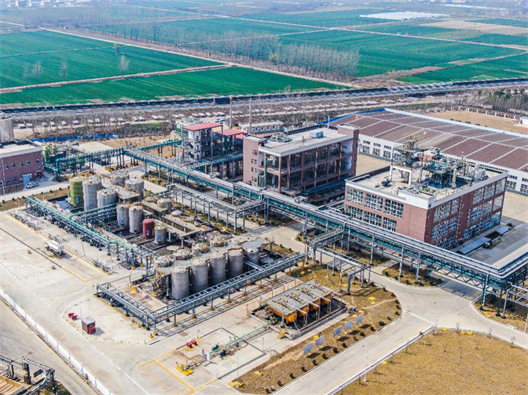
Figure 3: Industrialized Hydrogen Cyanide Plant Using DODGEN Technology
Considering that hydrogen cyanide is a highly toxic, volatile, and polymerizable compound, it cannot be stored, transported, or delivered over long distances. Therefore, hydrogen cyanide is essentially consumed on-site in the market, where it is used to synthesize its derivatives and other chemical products. For example, when producing hydroxyacetonitrile intermediates, iminodiacetonitrile, cyanohydrin (a methionine intermediate), or high-quality sodium cyanide or potassium cyanide, the first step requires ammonia removal units to treat the hydrogen cyanide synthesis gas, followed by reactions with different materials to obtain downstream products.Traditional ammonia removal methods use acid absorption towers to remove residual ammonia from the HCN synthesis gas. However, these methods have issues such as large equipment size, severe corrosion, and unsatisfactory results. DODGEN's high-efficiency ammonia removal technology replaces the acid absorption tower with a static mixing reactor, offering the following advantages compared to traditional acid absorption towers:
◆The static mixing reaction absorber has a small equipment volume and occupies less space, making maintenance and inspection convenient.
◆The addition of sulfuric acid and the extraction of ammonium sulfate during the ammonia removal process enable continuous and automated operation.
◆Gradient control of the sulfuric acid content and temperature in the three-stage absorption liquid improves ammonia removal efficiency and reduces equipment corrosion.
◆A high-efficiency gas-liquid separator is used to remove mist and foam from the tail gas, significantly reducing the sulfuric acid and ammonium sulfate carried into the subsequent products, improving the quality and yield of downstream products.
Throughout the entire lifecycle of an industrial hydrogen cyanide plant utilizing DODGEN's technology, an experienced expert team provides professional technical support to ensure customer benefits. With nearly 20 years of hydrogen cyanide operational experience and a large number of R&D projects, DODGEN possesses rich knowledge in hydrogen cyanide technology, ensuring that licensed plants operate safely, reliably, and efficiently.
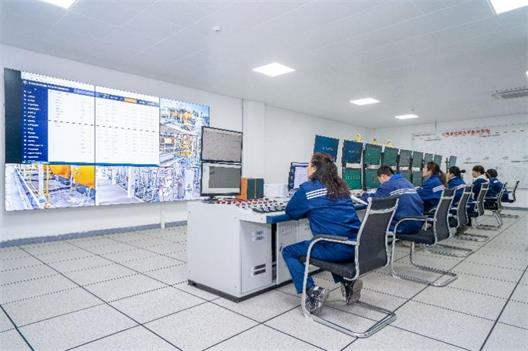
Figure 4 Central Control Room of Hydrogen Cyanide Plant Using DODGEN Technology
Conclusion
Hydrogen cyanide is not only an important factor in the origin of life but also serves as a precursor for many derivatives, most of which are fine chemical intermediates with significant applications in fields such as pharmaceuticals, pesticides, battery materials, and new energy. In recent years, China has made significant progress in the core production technology of the natural gas-hydrogen cyanide and its derivatives industry chain. The industry's capacity growth potential and profitability are highly promising. Particularly, breakthroughs in the technology and production of fine chemical products such as adiponitrile, Prussian blue, vitamins, and amino acids have driven technological advancements in related domestic industries. Hydrogen cyanide, as a key raw material, is expected to experience rapid growth in production as a result.