The recycling rate of PET waste plastics in China remains below 10% annually. The predominant recycling method is physical recycling, which, however, degrades the mechanical properties of PET, limiting the application scope of recycled PET products.
While physical recycling of PET is well-established, and the bottle-to-fiber recycling market is mature, bottle-to-bottle recycling must meet the stringent requirements of bottle manufacturing and food packaging. This has driven the development of chemical recycling technologies involving chain degradation and repolymerization. Chemical recycling involves converting PET molecular chains, where the polymer undergoes depolymerization into oligomers or monomers, followed by separation, purification, and other processes to serve as raw materials for producing chemical products. Significant advancements have been made in research and development of PET chemical recycling, including alcoholysis, enzymatic hydrolysis, and advanced recycling, some of which have achieved successful commercialization.
Chemical recycling can be carried out through hydrolysis, glycolysis, methanolysis, or saponification, resulting in various degradation products. This article focuses on the development and commercialization pathways of PET glycolysis.
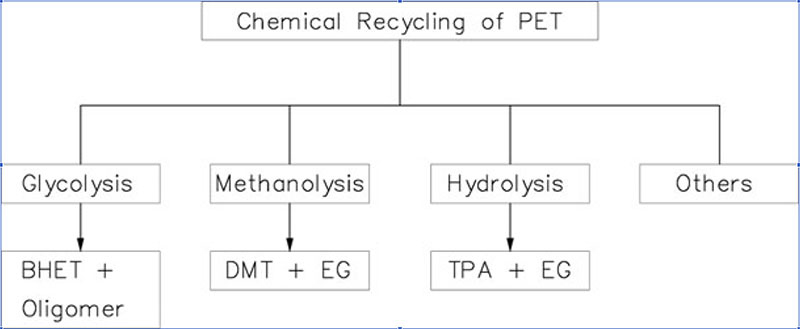
1. Commercialization Pathway for PET Glycolysis Recycling
DuPont has implemented methanolysis using Lewis acid as a catalyst. This process is suitable for recycling PET containing dyes, coatings, and other polymers. It is reported to have achieved a production capacity of 50,000 to 80,000 tons per year.
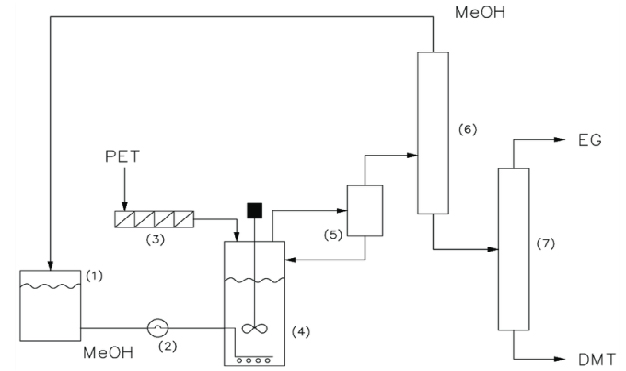
Goodyear (USA), DuPont (USA), and Hoechst (Germany) have successfully industrialized the EG glycolysis method. Fujita has also disclosed related technologies, proposing that shredded fabric should be pre-wetted with EG before entering the glycolysis system to facilitate and accelerate the glycolysis reaction.
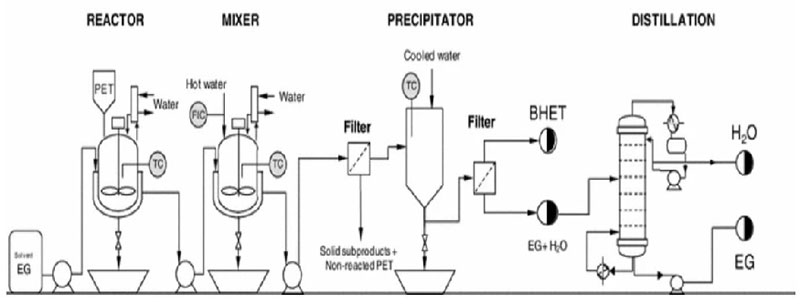
China's Zhejiang Jiaren Company, in collaboration with Japan's Teijin Corporation, has developed the ECO CIRCLE® technology. This technology can produce fine-denier fibers of the same quality as virgin PET and is suitable for recycling waste polyester garments containing dyes and pigments.
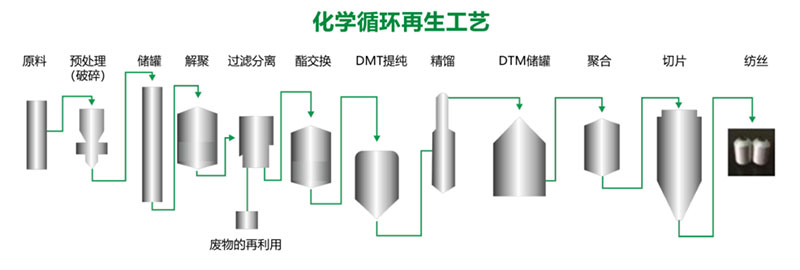
Saudi Arabia's SABIC is the industry's first supplier to use chemical upcycling methods to produce renewable PBT polyester, turning plastic waste into valuable resources.
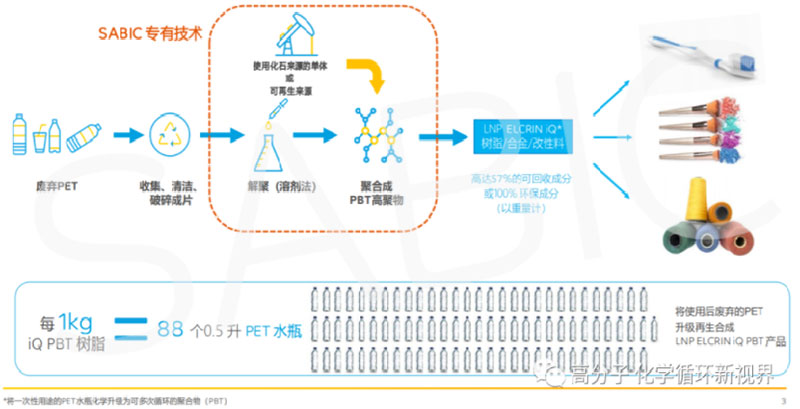
Eastman’s polyester renewal technology employs glycolysis or methanolysis to depolymerize waste into basic monomers, enabling the creation of new materials.
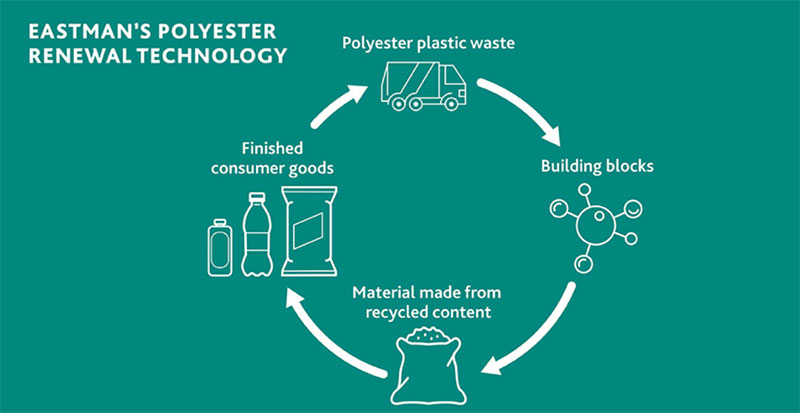
Guangdong Suiye Environmental Protection uses the ethylene glycol glycolysis method, employing ethylene glycol as a depolymerizing agent under high temperature and pressure to convert PET into BHET. BHET is then repolymerized into r-PET, r-PETG, pellets, and films.
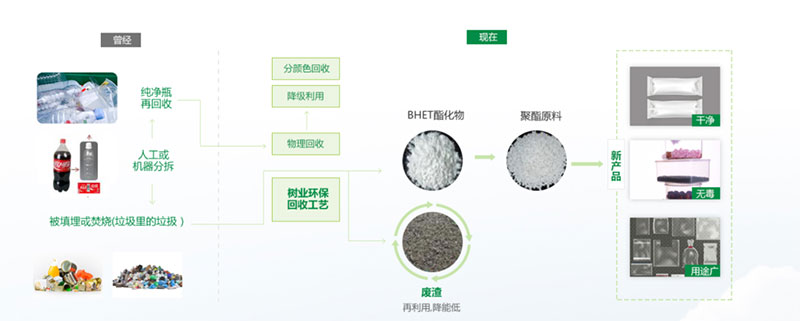
2. Main Issues with Glycolysis Method
The current PET glycolysis process is relatively complex. Whether using methanolysis or glycolysis, the crude products must undergo refining, filtration, and cleaning before being reused to produce recycled PET or other products. Since the primary depolymerization target products are BHET or DMT, the process involves deep depolymerization with long reaction times; high monomer purity requirements make separation and purification challenging; and the process is lengthy with high energy consumption. The following describes Eastman’s methanolysis process as an example:
This process involves degrading PET in methanol (MeOH) at a temperature of 180–280°C and a pressure of 2–4 MPa. The two main reaction products are DMT and EG, which are raw materials for synthesizing the original polymer. Methanolysis can proceed either through glycolysis followed by methanol transesterification or by directly placing PET in methanol. Early methods focused on liquid-phase methanolysis, whereas newer methods use methanol vapor by removing reaction products along with the solvent as vapor. In this approach, superheated methanol vapor passes through the reaction mixture, forming a melt containing low-molecular-weight polyesters, monomers, oligomers, glycols, and DMT.
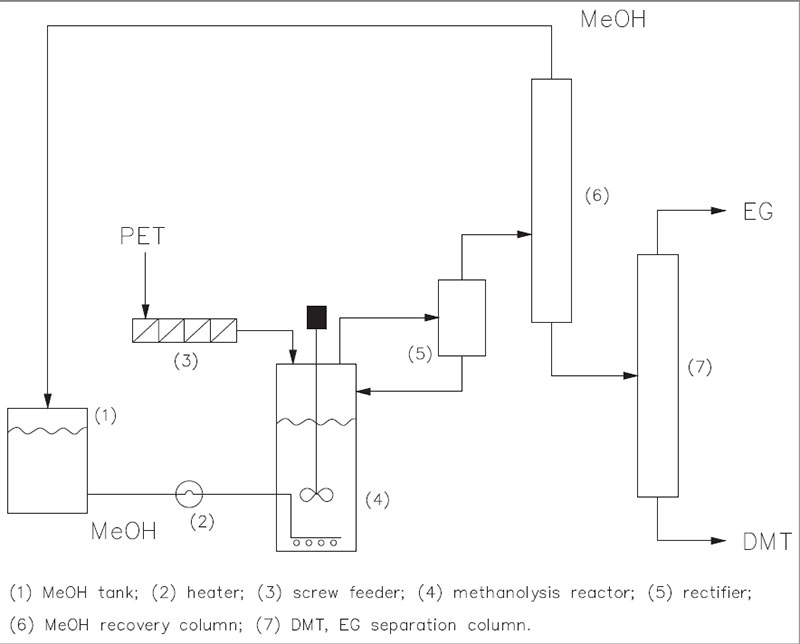
The primary advantage of vapor-phase methanolysis is that methanol serves not only as a depolymerizing agent but also as a carrier gas, separating the monomer components in the vapor phase from the oligomers in the liquid phase. Additionally, the reaction equilibrium shifts toward vapor-phase products, leading to a high DMT conversion rate of up to 90%. Furthermore, DMT, EG, and MeOH can be easily recovered and purified through distillation. However, pre-distilled DMT requires further purification via crystallization to remove critical impurities that negatively impact its repolymerization behavior. These impurities include water, diols, alcohols, catalysts, and closely related vapor-phase components, such as phthalate derivatives (e.g., dimethyl isophthalate, DMI).
3. Purification of DMT, EG, and Methanol
As noted above, methanolysis degrades low-quality feedstock into DMT and EG. However, the commercial potential of recycled PET is constrained by quality standards for reuse in food packaging. Therefore, the purity of raw materials is crucial. Methanol can be purified by boiling it off from the reactants EG and DMT, followed by distillation. However, due to the DMT-EG azeotrope, separating EG and other diols from DMT through distillation is more challenging and requires extensive theoretical studies.
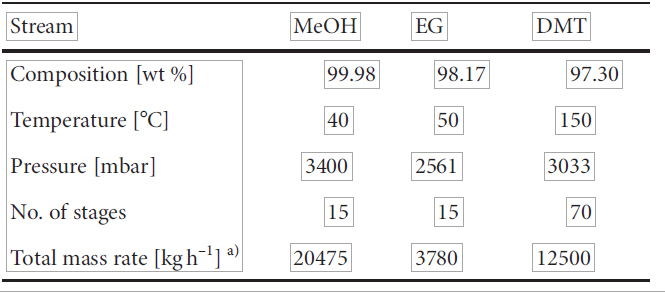
MeOH, EG, and DMT Separation Column
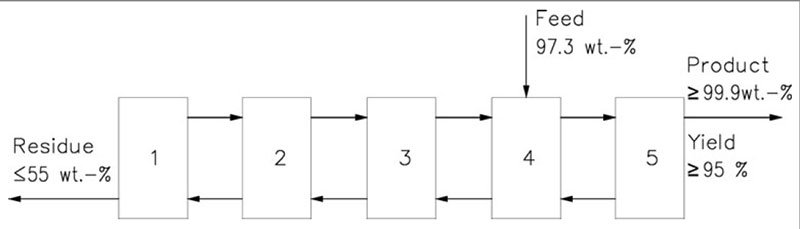
Separation reaction PRO/II simulation results for products
Table 1 presents the PRO/II design and simulation results for separating reaction products via distillation. The data indicate that vacuum distillation can achieve high-purity methanol and ethylene glycol. However, pre-distilled DMT has a purity of 97.3 wt% and requires further processing to meet the quality standards for bottle-grade PET. This can be achieved through recrystallization in a methanol solution or solvent-free melt crystallization.The traditional recrystallization process involves the use of DMT crystallizers, DMT centrifuges, DMT melters, and filters, along with a significant amount of methanol as a solvent. The associated crystallization equipment and solvent recovery units typically account for 45% of the total investment cost. In contrast, solvent-free melt crystallizer improves operational flexibility and reduces the potential investment and operational costs of commercial facilities.
Many organic materials are purified through crystallization, where the feed mixture generally has a high concentration of crystalline components. Crystallization in such mixtures differs from conventional solution crystallization and is thus referred to as melt crystallization. Here, the melt is defined as a liquid that solidifies upon cooling within a relatively narrow temperature range, close to the melting point of the primary crystalline component. The primary purpose of this process is purification rather than particle formation.
A pilot-scale falling-film crystallizer, equipped with an 18-meter-long vertical tube, was used for melt crystallization of synthetic DMT mixtures containing multiple impurities. This system is eutectic, with a eutectic temperature of 55°C for a mixture containing 9 wt% DMT. Therefore, on the DMT side of the phase diagram, the total impurities can be treated as a single impurity. Upon cooling, DMT crystals grow from the falling film of the melt inside the cooling tube. Impurities such as water, diols, alcohols, catalysts, and non-PET components from copolymers (e.g., DMI, bisphenol A, and caprolactam) are excluded from the crystals and concentrated in the mother liquor. Further cooling results in layered growth, followed by the discharge of impure melt.
The crystallized layer is further purified through partial melting (a process known as sweating), which is similar to the washing step in solution crystallization. The purified crystalline layer is then melted (at a melting point of 142°C) to recover a pure liquid product.
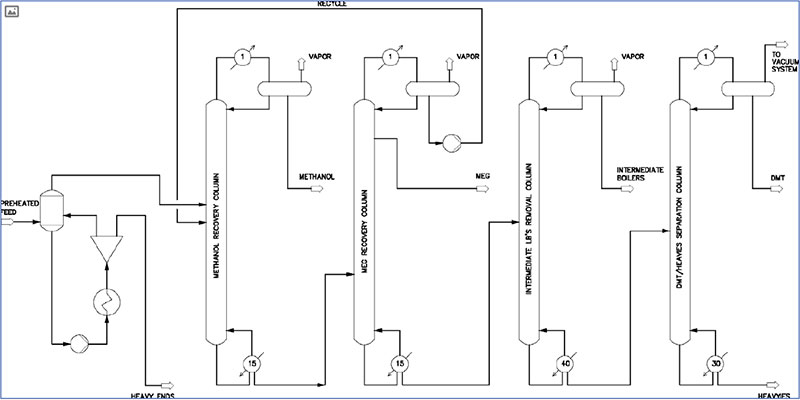
Separation stages for high-purity DMT production
Layer crystallization purification is carried out through repeated temperature cycles and mass balance adjustments during specific separation stages. The cyclic nature of the process allows multiple separation stages to be performed in a single crystallizer. This enables achieving the desired product purity of over 99.9 wt% DMT without compromising recovery rates. Similarly, by adding stripping stages, the DMT content can be increased to over 95%, thereby minimizing product losses. It should be noted that higher initial crystal purity results in better separation efficiency, which decreases as impurity levels rise.
Falling-film crystallization is typically used for relatively pure feedstock and high-capacity operations. As a result, crystallization times are shorter, with 40 to 60 minutes required to crystallize approximately 80% of the initial mass. The final thickness of the cylindrical crystal layer ranges from 8 to 12 mm. Sweating times are even shorter, typically between 15 and 20 minutes, with the final crystal mass retaining 50% to 95% of the initial mass, depending on the initial purity.
One of the main advantages of layered crystallization is that no mechanical devices are required to transport liquid fractions. The only moving components in the process are standard pumps and valves. However, recovering a pure liquid product requires the material to remain relatively stable at its melting point. DMT readily meets this requirement. Donggong’s ongoing research into melt crystallization purification has achieved exceptionally high product purity, significantly enhancing the sustainability of PET chemical recycling.