In recent years, with the rapid advancement of Industry 4.0, the manufacturing industry has ushered in an unprecedented wave of transformation, and digitalization has become an indispensable "engine" of the new industrial era. DODGEN seizes this opportunity, leveraging leading technologies and a strict pursuit of quality to establish a benchmark in digital equipment manufacturing, injecting intelligence and vitality into precision manufacturing.
【Digital Empowerment, Precision at Its Peak】
DODGEN (Chongqing) Energy Equipment Co., Ltd. is the manufacturing base for DODGEN's core equipment and key components, tasked with the mission of precisely realizing design concepts. Stepping into DODGEN's workshop, digital operations come into view, with advanced domestic and international equipment efficiently running under the command of CNC systems, significantly enhancing production efficiency.
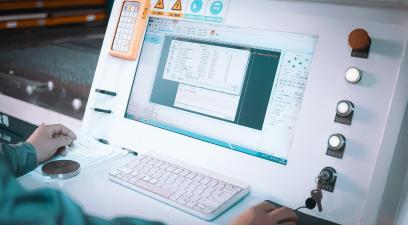
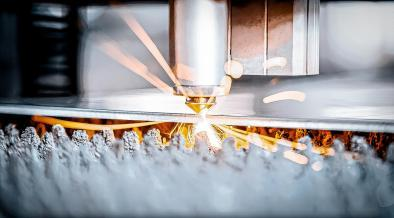
Taking the cutting process as an example, traditional methods require extensive manual grinding, which is inefficient and causes significant pollution. In contrast, DODGEN uses automated cutting machines, which not only improve efficiency but also result in smoother and more refined cutting surfaces.
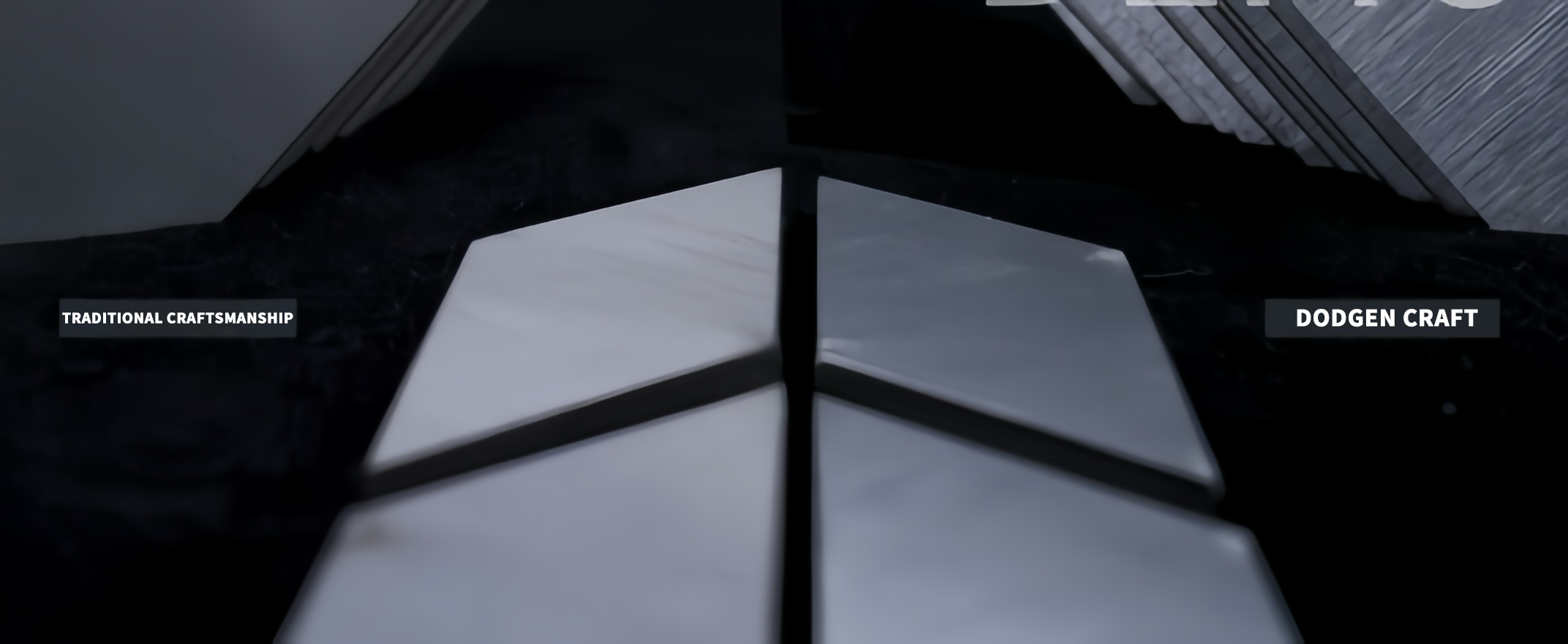
Similar innovations are also reflected in the bending process, where DODGEN uses CNC-operated bending machines, ensuring high-precision processing and significantly improving efficiency. Additionally, in plate rolling, DODGEN employs CNC four-roll machines, which ensure precise product roundness without the need for secondary rounding adjustments.
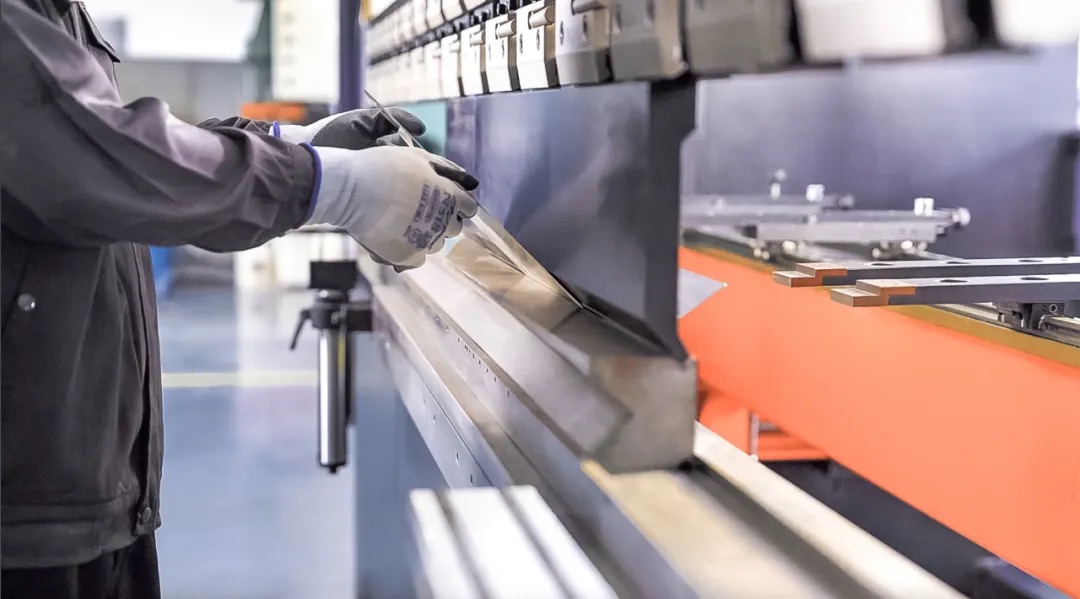
In the filler production area, the 1+3 automated production line demonstrates DODGEN's industrial digitalization strength. While traditional factories require 13 workers for operation, DODGEN's automated process involves minimal human intervention, reducing human-machine contact, enhancing safety, and improving production stability.
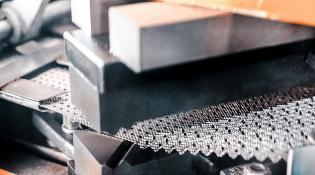
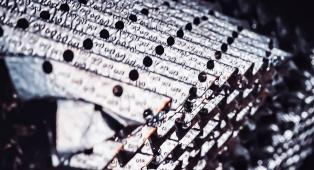
【Strict Quality Control: The Gold Standard of DODGEN Quality】
Quality is the lifeline of a business, and at DODGEN, this philosophy runs through every step, from raw material procurement to finished product delivery. By digitally recording each production stage, DODGEN ensures comprehensive product quality assurance. Every process in the workshop, from raw material feeding and welding to final assembly, strictly follows standardized operating procedures. Professional inspectors and high-precision testing equipment serve as a strong safeguard, providing the final assurance for product quality.
For example, with DSR components, DODGEN not only sources high-quality raw materials from renowned suppliers but also conducts physical and chemical re-inspections to ensure exceptional performance. The saturation of the DSR bent pipe section far exceeds national standards, with low fluid resistance and high material throughput, making it less prone to blockages during material flow.
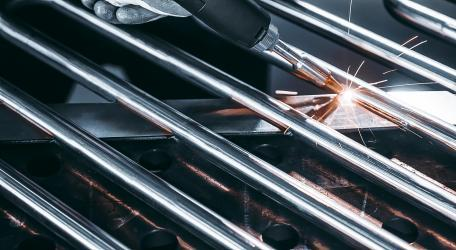
In addition, for the melt crystallization equipment's membrane head, DODGEN employs the 6S management model and Kingdee Cloud System in production, strictly controlling welding quality and process precision. Compared to the 5%–7% rework rate of traditional manufacturers, DODGEN's defect rate is below one in ten thousand.
【Precision Craftsmanship Builds the Brand】
With rich experience, strong technical expertise, standardized management processes, high-precision equipment, and a comprehensive quality management system, DODGEN combines deep investment and deployment in innovation, research and development, process design, and pilot testing stages to provide customers with outstanding engineering project incubation services.