The cyanide-containing tail gas produced as a byproduct in the carbon fiber production process is a highly dangerous and toxic gas that causes severe environmental damage and poses a significant threat to human health. The common methods for treating cyanide tail gas in carbon fiber production are incineration and adsorption. In both cases, the harmful components in the exhaust gas are ultimately destroyed through incineration. Although incineration can break down these harmful substances, it also generates pollutants such as nitrogen oxides, and the treated exhaust still requires further nitrogen removal and other measures to meet emission standards. This method leads to secondary environmental pollution and, to some extent, causes resource waste.To address this issue, DODGEN proposes a treatment process that focuses on the resource utilization of cyanide-containing tail gas in carbon fiber production. This process involves the comprehensive utilization of valuable components, such as HCN and NH3, in the exhaust gas. After treatment, the tail gas meets emission standards, and the byproducts are used to produce downstream cyanide-based fine chemicals, resulting in significant economic benefits.
I. Technical Background
Carbon fiber has excellent properties such as high strength, high temperature resistance, corrosion resistance, fatigue resistance, creep resistance, and electrical and thermal conductivity. It is widely used in aerospace, sports and leisure, medical, and civil engineering fields, making it a high-performance fiber material for both military and civilian applications. Currently, carbon fiber production primarily uses polyacrylonitrile (PAN) as the raw material, undergoing two key steps—oxidation and carbonization—to produce carbon fibers with high carbon content. However, during the oxidation and carbonization stages, a large amount of tail gas is generated. The tail gas contains low levels of combustible components, requiring the addition of fuel for harmless incineration. As a result, fuel consumption is high, leading to increased operational costs. The main pollutant in carbon fiber tail gas, hydrogen cyanide, is an extremely dangerous and toxic substance, with a toxicity 35 times that of carbon monoxide. Direct emission of this pollutant severely contaminates the air, posing a significant threat to human health.
Currently, most of the tail gas generated during the carbon fiber production process is treated by combustion or adsorption methods. A typical approach is the use of a Regenerative Thermal Oxidizer (RTO) [5]. However, this method operates at high temperatures, consumes a large amount of fuel, results in high operating costs, and generates significant exhaust gas. The treated HCN does not meet industrial pollutant emission standards ( <0.3 mg/m³), and some HCN and NH₃ are oxidized into nitrogen oxides, leading to secondary air pollution. Furthermore, this method does not utilize the tail gas in a comprehensive way or produce valuable byproducts for downstream use.
For carbon fiber tail gas with high concentrations of HCN and tar, on one hand, the combustion method fails to meet emission standards, leading to environmental pollution, which is detrimental to carbon fiber production. On the other hand, it does not make comprehensive use of the tail gas or produce valuable byproducts for downstream applications, resulting in energy waste. Therefore, how to treat and utilize carbon fiber tail gas in a comprehensive manner is crucial for reducing energy consumption, alleviating environmental pressure, and saving production costs. To address this, DODGEN has developed a set of equipment for treating cyanide-containing tail gas generated during the oxidation and carbonization stages, achieving good results in the treatment of carbon fiber cyanide tail gas.
II. Carbon Fiber Process Flow
The simplified diagram of the carbon fiber process flow is shown below:
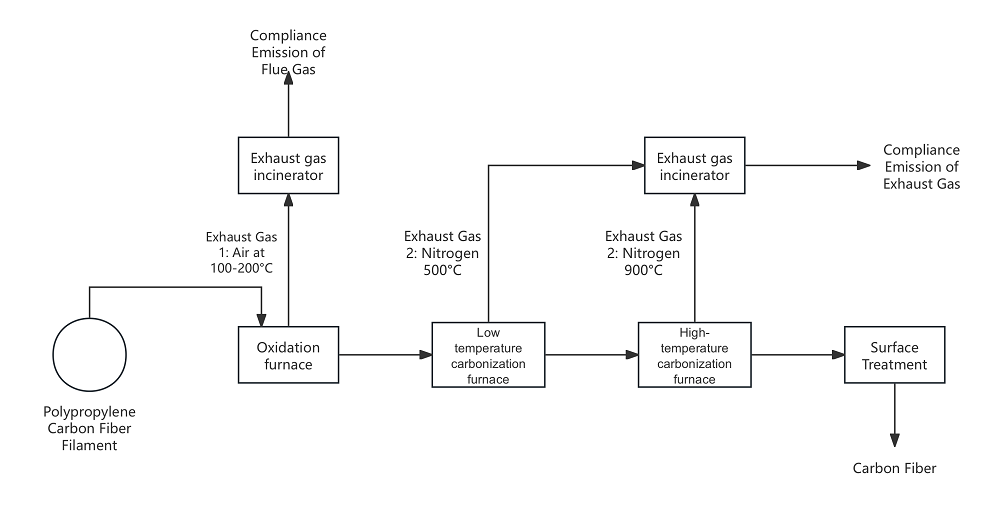
Figure 1: Simplified Diagram of the Carbon Fiber Process Flow
As shown in the diagram, the tail gas temperature during the carbonization stage is higher (500-900°C), and the exhaust gas volume is lower compared to the oxidation stage. Therefore, the concentration of organic compounds in the tail gas is higher, and it releases toxic and harmful gases such as HCN, NH₃, and contains some tar. In the oxidation stage, the total volume of tail gas is larger, with temperatures ranging from 100-200°C. The concentration of toxic and harmful gases like HCN and NH₃ is low (less than 0.1%). It is estimated that for every ton of carbon fiber produced, 1 ton of organic compounds is generated, including 200-300 kg of tar and 300-400 kg of HCN.
III. Process Flow and Treatment Results
1. Raw Materials
The raw material consists of the waste gas generated during the oxidation and carbonization processes in a carbon fiber factory with an annual production capacity of 2000 tons of carbon fiber. The composition and mass concentration of the waste gas are shown in Table 1 and Table 2.
Table 1: Mass Concentration of Each Component in Oxidation Furnace Tail Gas

As can be seen from Table 1 above, due to the large total gas volume, the overall concentration of organic compounds is less than 0.1%.
Table 2: Mass Concentration of Each Component in Carburetor Tail Gas

The exhaust gas from the oxidation furnace and the carbonization furnace must be treated and discharged separately due to significant fluctuations in concentration when mixed, as well as issues with dilution during discharge.
2. Analytical Methods
Table 3: Analytical Methods for Key Pollutants
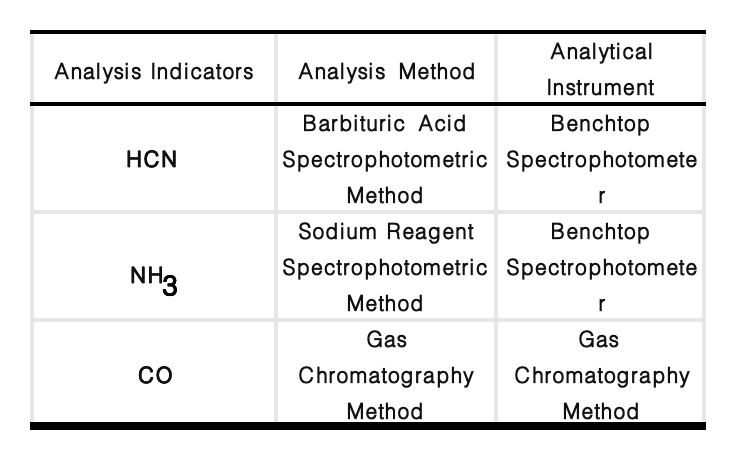
3. Oxidation Furnace Exhaust Gas Treatment
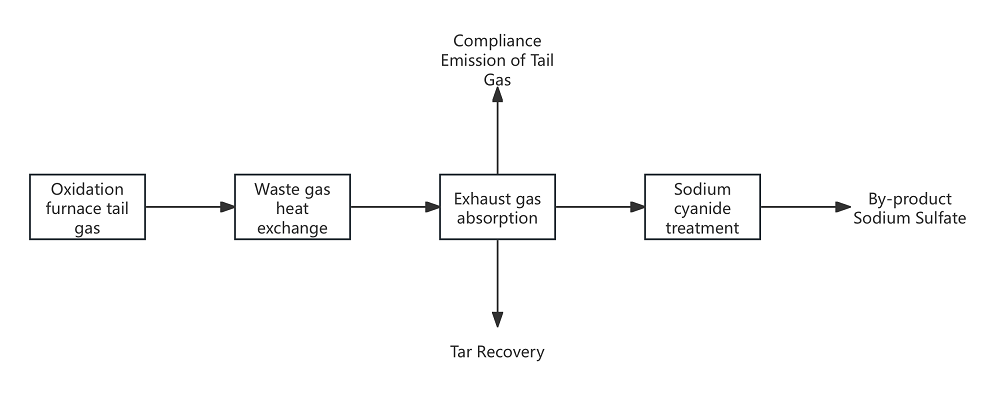
Figure 2: Oxidation Furnace Exhaust Gas Treatment Process Flow
The hot air from the oxidation furnace has a temperature ranging from 100-200°C, which requires preheating. Based on the pollution characteristics of the exhaust gas, a three-stage absorption tower is selected for absorption treatment. Each tower is equipped with a circulating pump, and the circulating liquid is sprayed from the top of the tower to ensure full contact between the liquid and the exhaust gas, allowing for the removal of pollutants from the exhaust. Sodium cyanide at a concentration of 10% can be concentrated to 30% and sold as a product. However, selling sodium cyanide separately may be difficult due to the regulatory issues surrounding the sale of highly toxic chemicals. Therefore, a sodium cyanide process involving sulfuric acid to acidify sodium cyanide is used to convert it into hydrogen cyanide (HCN), which is then used to produce hydroxyacetonitrile.
Reaction formula for sodium cyanide treatment:
NaCN+H2SO4→HCN+NaSO4
4. Carbonization Furnace Exhaust Gas Treatment
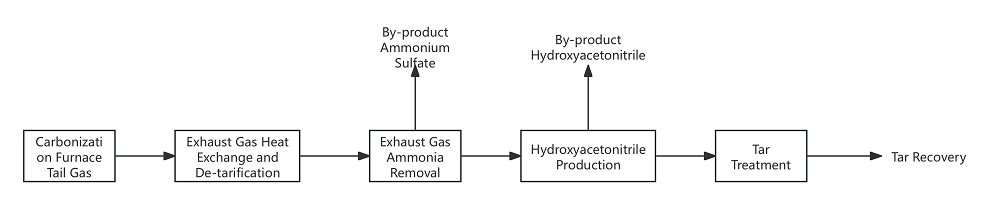
Figure 3: Carbonization Furnace Exhaust Gas Treatment Process Flow
The waste gas composition from the low-temperature carbonization furnace and the high-temperature carbonization furnace is similar, and both have relatively high temperatures. Therefore, it is considered to treat both streams of exhaust gas together after mixing. The exhaust gas from the high-temperature carbonization furnace (about 900°C) and the low-temperature carbonization furnace (about 600°C) is mixed in the pipeline and enters the heat exchanger at a temperature of about 500-600°C for heat exchange. Since tar has high viscosity at lower temperatures, a solvent is used to mix and absorb the tar. The exhaust gas, after tar removal, is sent to a three-stage ammonia removal system to eliminate ammonia from the exhaust. The final product is an ammonium sulfate solution, which is sent out for ammonium sulfate recovery. The ammonia removal process utilizes the neutralization reaction between ammonia and sulfuric acid in the aqueous solution to remove ammonia from the exhaust. The reaction equation is as follows:
H2SO4+2NH3→(NH4)2SO4+H2O
Formaldehyde and HCN-containing exhaust gas enter the hydroxyacetonitrile reactor, where they react with the circulating liquid to produce hydroxyacetonitrile. The exhaust gas, which contains combustible substances such as CO and H₂, is then sent to a tail gas incinerator for combustion. The hydroxyacetonitrile produced in this process can be used as an intermediate to manufacture other products or sold as a product. The hydroxyacetonitrile process involves the reaction of formaldehyde solution with HCN to generate hydroxyacetonitrile. The chemical reaction equation is as follows:
HCN+HHCHO→HOCH2CN
The tar from the carbonization section and the oxidation section is simultaneously fed into the solvent removal tower and HCN stripping tower to recover the tar.
5. Treatment Results and Economic Benefits
The flow rates and concentrations of HCN, NH₃, and CO in the exhaust gases from the oxidation furnace and mixed carbonization furnace exhaust, as well as the flow rates and concentrations of HCN, NH₃, and CO in the exhaust gas discharged into the atmosphere, were detected using the aforementioned analytical methods. The results are shown in Table 4.
Table 4: Treatment Efficiency of Key Pollutant Gases in the Oxidation Furnace
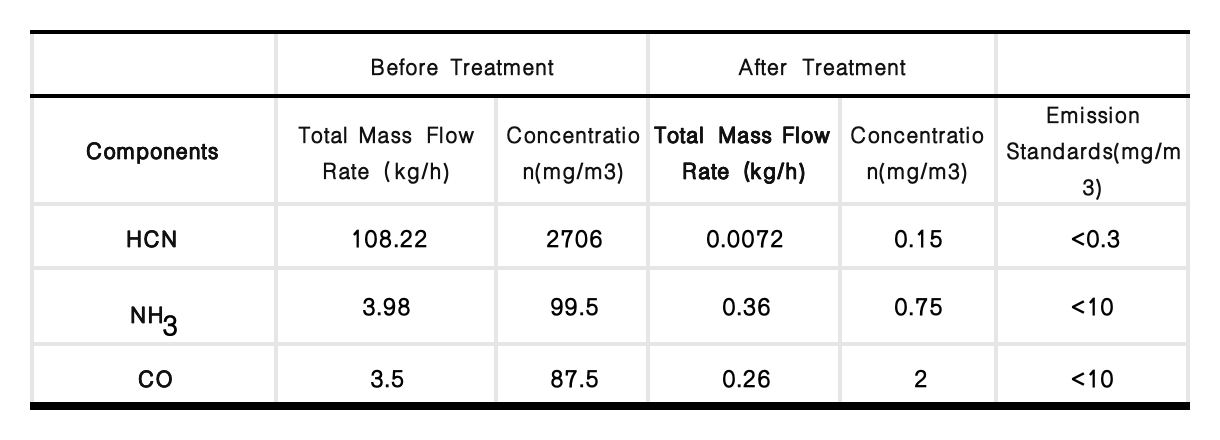
Table 5: Treatment Efficiency of Key Pollutant Gases in the Carburetor
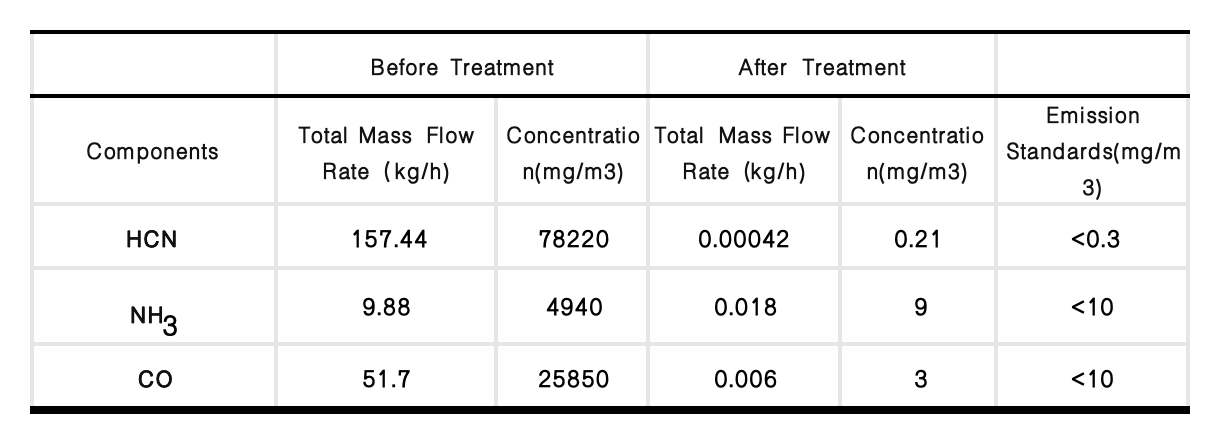
As shown in Tables 4 and 5, this process can effectively adapt to the variations in the concentration of various components in cyanide-containing tail gas from carbon fiber production, and it can still achieve compliance with emission standards after treatment. Based on a production capacity of 2000 tons per year, the cyanide tail gas treatment can produce 1860 tons per year of hydroxyacetonitrile (on an annualized basis), 140 tons per year of ammonium sulfate, and 560 tons per year of tar. Since this project involves a single 2000-ton carbon fiber production line, the byproduct, hydroxyacetonitrile, is sold as a product. The comprehensive utilization of exhaust gas from 2000 tons of carbon fiber is expected to generate economic benefits exceeding 25 million RMB. For larger-scale carbon fiber production, the hydroxyacetonitrile industry chain can be further extended to include higher value-added products such as imidazolidine diethanolamine, iminodiacetic acid, glycine, hydroxyacetic acid, and diphosphate, among others.
IV. Conclusion
(1) This process can effectively accommodate large fluctuations in both the temperature and concentration range of cyanide-containing tail gas from carbon fiber production. It has strong adaptability, requires minimal fuel consumption, and the production system can operate continuously and stably. The process is simple to operate.
(2) After treatment of the cyanide-containing tail gas from carbon fiber production, the HCN concentration can meet the emission standards set by the "Comprehensive Emission Standards for Air Pollutants" (GB16297-1996), NH₃ can meet the "Ambient Air Quality Standards" (GB3095-2012), and CO can meet the "Ambient Air Quality Standards" (GB3098-2012).
(3) This process successfully converts HCN in the cyanide-containing tail gas from carbon fiber production into hydroxyacetonitrile, a product with higher economic value, and converts NH₃ into fertilizer-grade ammonium sulfate. It also recycles tar. It is estimated that the byproducts, including hydroxyacetonitrile, from the exhaust gas of 2000 tons of carbon fiber can generate sales revenue of over 25 million RMB, demonstrating significant economic benefits.