In September 2024, global chemical giant Trinseo announced the closure of its polycarbonate (PC) production plant in Stade, Germany. Production is expected to cease by January 2025, after which the company plans to source downstream PC compounded products externally, saving an estimated $15–20 million annually.
According to statistics, Trinseo’s German PC plant has an annual production capacity of 160,000 tons, making it the second-largest PC producer in Germany after Covestro. Researchers have attributed the decision to close the plant to fluctuations in raw material costs, which have significantly impacted profit margins.Notably, raw material costs account for over 69% of the total cost structure of PC, making it the largest cost component. Utilities rank second, contributing approximately 24% to the total unit cost. In contrast, other expenses such as additives, catalysts, waste treatment, labor, and management have relatively minor shares.
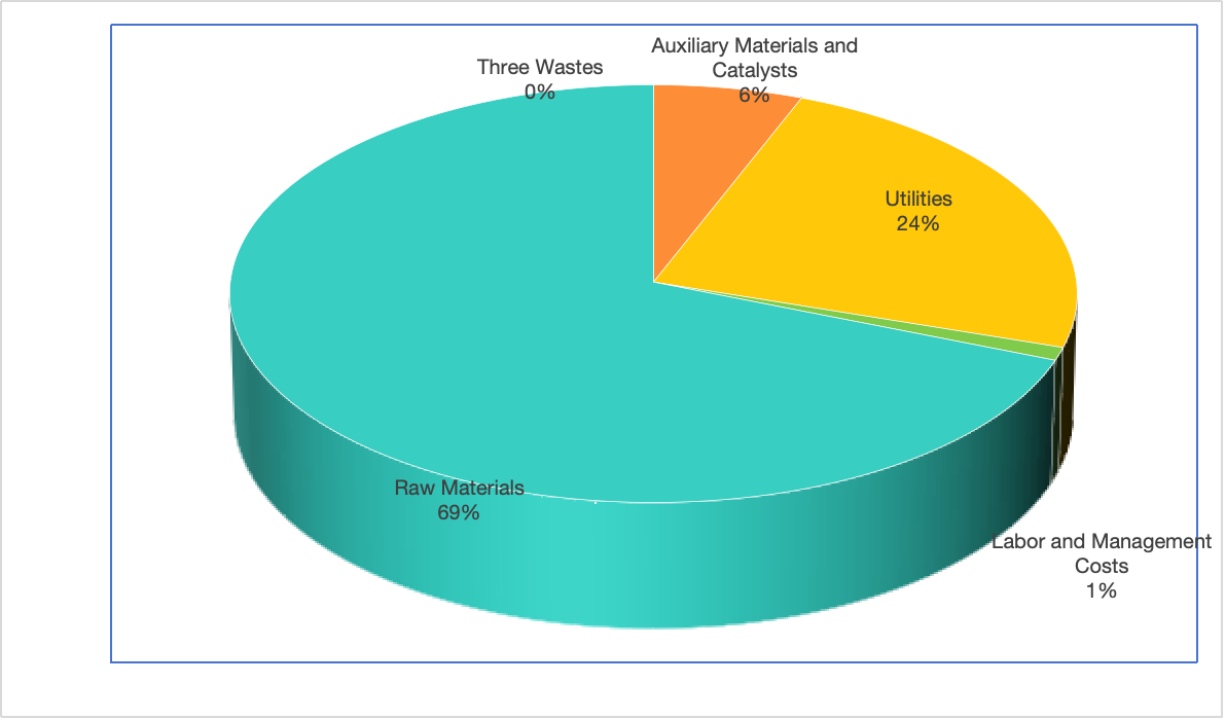
Figure 1: Cost Structure Proportion of Polycarbonate (PC)
For raw materials in non-phosgene polycarbonate (PC) production, bisphenol A constitutes the largest portion of raw material costs, accounting for approximately 83%. Dimethyl carbonate (DMC) and phenol follow, contributing 15% and 2%, respectively. Fluctuations in bisphenol A prices have an impact exceeding 57% on PC costs, making it the primary and most significant cost factor.
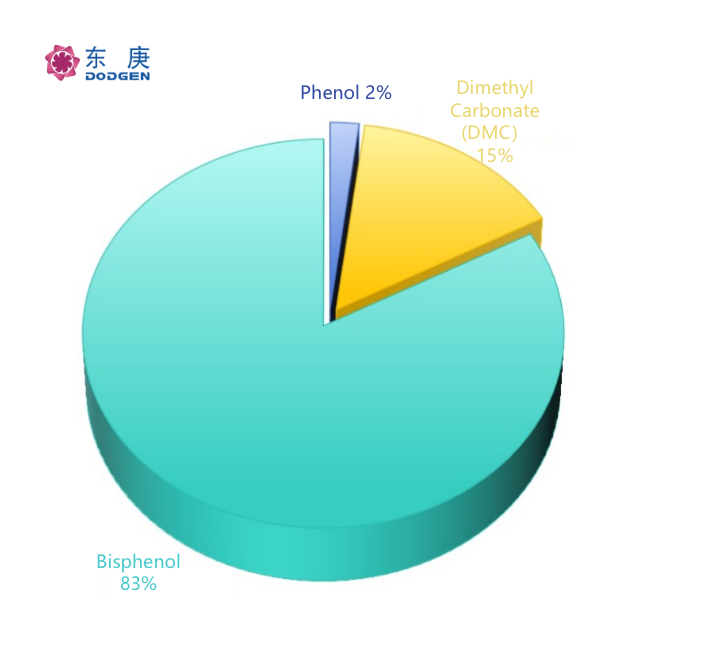
Figure 2: Proportion of PC raw material cost composition
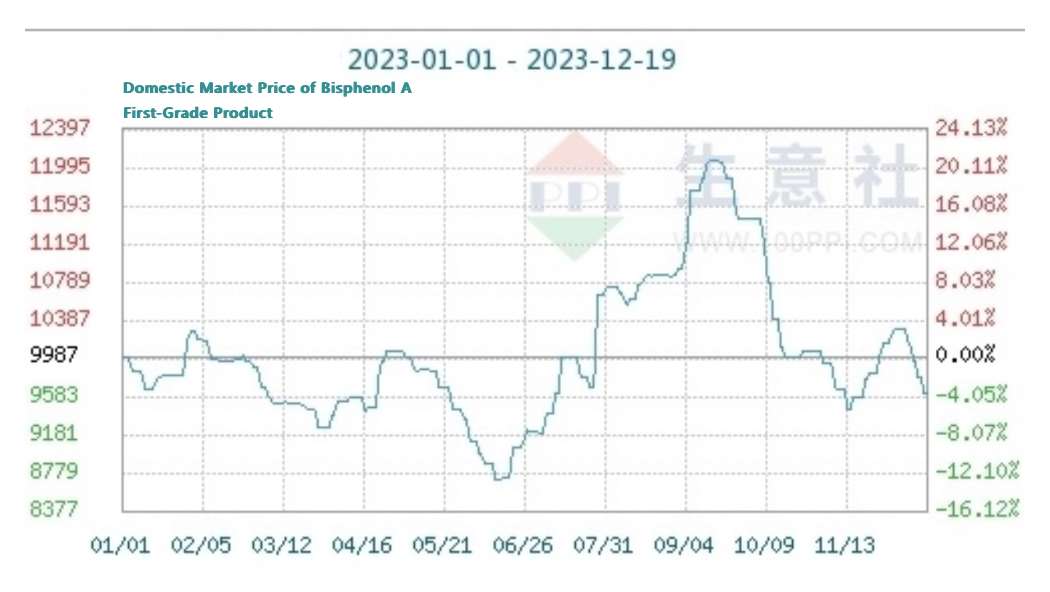
Figure 3: Domestic Bisphenol A Market Prices in 2023
According to data from Business Society, bisphenol A market prices have fluctuated significantly since 2023, resembling a “roller coaster” trend overall. As of early October 2024, the average market price of bisphenol A in China has fallen below 10,000 yuan per ton. However, since the price drop is not substantial, it has failed to significantly boost PC profit margins, which may be one of the main reasons Trinseo decided to exit the PC market.
Currently, the main production processes for PC are the phosgene method and the non-phosgene transesterification method. A new green production process involves using bio-based isosorbide as a raw material to produce PC through transesterification polycondensation. At present, Mitsubishi Chemical in Japan is the only company that has successfully commercialized the production of bio-based polycarbonate. Unlike bisphenol A, bio-based isosorbide is an aliphatic compound with high safety, making it highly promising for applications in areas such as food packaging, baby bottles, and medical devices.
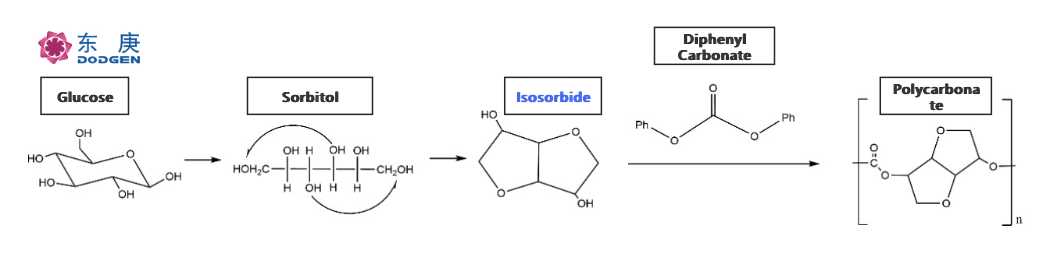
Figure 4: Technological pathway for synthesizing polycarbonate from glucose
Mitsui Chemicals and Mitsubishi Gas Chemical Company (MGC) were the first to achieve the commercial production of bio-based polycarbonate (PC) copolymers using isosorbide. Mitsubishi Chemical states that DURABIO offers superior optical properties and impact resistance compared to traditional PC resins. Unlike bisphenol A, isosorbide is an aliphatic compound.In addition to its high transparency and optical uniformity, this PC resin only undergoes slight yellowing when exposed to light. Its high transparency makes it easy to color, even for deeper shades and metallic finishes.
Isosorbide is a bio-based raw material that can replace bisphenol A in the production of polycarbonate (PC). It is derived by extracting glucose from various biomass sources, catalytically hydrogenating glucose to produce sorbitol, and then catalytically dehydrating sorbitol to obtain isosorbide. Isosorbide can significantly enhance the performance of polycarbonate, polyurethane, polyester, and epoxy resins in diverse applications such as packaging, automotive, coatings, and adhesives. Additionally, due to its bio-based nature, synthesizing PC with isosorbide supports downstream industries in achieving net-zero carbon emission targets.
Global chemical leader SABIC has introduced LNP™ ELCRIN™ EXL7414B copolymer, its first bio-based polycarbonate (PC) copolymer, which helps the consumer electronics industry achieve net-zero carbon goals while advancing SABIC’s sustainability strategy. This bio-based PC is also SABIC’s first product to achieve International Sustainability and Carbon Certification (ISCC+) status. According to the mass balance approach, over 50% of the bio-based content in its formulation is sourced from waste materials. Compared to fossil-based alternatives, every kilogram of this new bio-based resin reduces carbon dioxide emissions by two kilograms. This innovative bio-based PC has already been successfully applied in smartphone battery covers, enabling end customers to achieve competitive differentiation and stronger sustainability efforts.
The broad adoption of bio-based PC relies on the development of upstream raw materials. As an excellent bio-based raw material, isosorbide is primarily derived from sorbitol, which is widely available, cost-effective, and environmentally friendly. As a result, isosorbide is regarded as the second most promising bio-based chemical material after polylactic acid, with substantial commercial potential.In the pharmaceutical field, isosorbide serves as an effective osmotic oral diuretic and is also used in the preparation of drugs like isosorbide dinitrate and isosorbide mononitrate. In the plastics field, citrate-based plasticizers synthesized from isosorbide and citric acid represent a new class of green, environmentally friendly plasticizers that can replace traditional ones such as phthalate-based plasticizers.
