Extraction separates mixtures based on the differing solubilities of substances in immiscible solvents. The extraction-crystallization process can be understood as the coupling of “extraction” and “crystallization.” Its principles fall into two categories:
1. The interaction between the extractant and solvent is stronger than that between the target product and solvent. This interaction reduces the solubility of the target product, causing it to precipitate through crystallization.
2. Melt crystallization utilizes differences in the freezing points of the components in a substance to achieve separation and purification. By precisely controlling the input and removal of heat, the desired component crystallizes out of the molten mixture. Subsequent operations like washing and sweating further refine and purify the target component.
The coupled process of melt crystallization and extraction combines the advantages of both methods. It initially separates the target substance through extraction and then further purifies it via melt crystallization.
Many researchers have successfully applied this coupled process to the separation and purification of various substances, achieving excellent results.
In the study of the extraction-coupled melt crystallization process for 2,6-dimethylnaphthalene in coal tar, the typical procedure involves the following steps:
1. Pre-treatment: Coal tar undergoes distillation to isolate the fraction containing 2,6-dimethylnaphthalene.
2. Extraction: A specific extractant is used to extract the pre-treated fraction, increasing the concentration of 2,6-dimethylnaphthalene. This step typically takes place in a liquid-liquid extraction column, where selective solubility of the solvent enables component separation.
3. Vacuum Distillation: The extracted solution undergoes vacuum distillation to further concentrate 2,6-dimethylnaphthalene and remove low-boiling impurities.
4. Melt Crystallization: The concentrated solution is subjected to melt crystallization under controlled conditions. Differences in melting points between 2,6-dimethylnaphthalene and other components are utilized to crystallize the target compound.
5. Separation and Washing: The crystallized solid is separated via filtration or centrifugation and washed to remove remaining impurities.
6. Refinement: The washed crystals may undergo one or more recrystallization steps to further improve purity.
7. Drying: Finally, the crystals are dried to remove any residual solvents or mother liquor, yielding high-purity 2,6-dimethylnaphthalene.
Specific process conditions, such as temperature, pressure, solvent type, and operation time, must be optimized based on actual conditions. In practical applications, additional steps may be incorporated, such as using complexing agents to enhance the separation efficiency of 2,6-dimethylnaphthalene or employing membrane separation techniques for further purification.
In a 2019 study by Ban et al., researchers first used vacuum distillation to enrich coal tar fractions, achieving a 2,6-dimethylnaphthalene concentration of 11.56%. Melt crystallization was then employed to remove isomeric impurities. Ultimately, they obtained dimethylnaphthalene with a purity of 62.64% and a yield of 68.12%. This process demonstrated the effectiveness of coupling vacuum distillation with melt crystallization for extracting and purifying 2,6-dimethylnaphthalene from coal tar.
In the production of 4-aminodiphenylamine, phenazine, a valuable byproduct, can be efficiently separated and purified using the coupled process of extraction and melt crystallization. Below is a detailed process plan:
1. Extraction: The waste liquid from 4-aminodiphenylamine production undergoes an extraction process using a suitable extractant to concentrate phenazine. This step aims to increase the phenazine concentration, facilitating subsequent separation and purification.
2. Melt Crystallization: The extracted solution is subjected to melt crystallization under controlled temperatures. Due to the difference in melting points between phenazine and other components, phenazine crystallizes out preferentially during gradual cooling.
3. Separation: The crystallized phenazine is separated from the solution through filtration or centrifugation.
4. Washing: The phenazine crystals are washed to further remove impurities.
5. Drying: The washed phenazine crystals are dried under controlled conditions to eliminate residual solvents.
6. Refinement: Additional crystallization steps may be performed to further enhance the purity of phenazine.
In a 2015 study by Li et al., crude phenazine was separated from waste liquid using melt crystallization. Impurities in the crude phenazine were then removed through an extraction process, and final recrystallization yielded phenazine with a purity of 99.5% and a recovery rate of approximately 85%. The process flow is shown in the diagram below.This method not only improved the purity and yield of phenazine but also reduced environmental pollution and production costs.
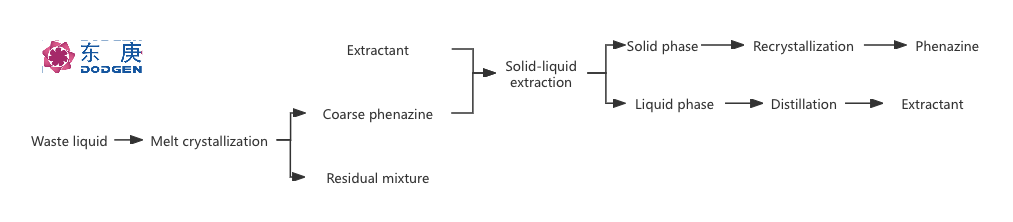
This coupled process of extraction and melt crystallization effectively recovers and purifies phenazine from the waste liquid generated during 4-aminodiphenylamine production, showcasing significant industrial application value.
The combined method offers advantages such as low energy consumption, short operation cycles, and minimal environmental impact from the extraction process, while also benefiting from the high separation efficiency of melt crystallization. This coupling simplifies the workflow and enhances separation performance.DODGEN leverages advanced melt crystallization and extraction technologies to provide customized solutions tailored to client needs, ensuring optimal separation results.