Compared with other separation processes, melt crystallization offers advantages such as simplicity of operation, low energy consumption, cost efficiency, mild operating conditions, wide applicability, and environmental friendliness. These advantages have facilitated its further development. However, when applied to industrial production, melt crystallization also has limitations, such as long production cycles and complex equipment, which restrict its advancement. To further optimize the separation process, the coupling of melt crystallization with other separation techniques such as distillation, extraction, solution crystallization, and membrane separation can be considered. This approach can yield higher-quality products and achieve better separation performance.
1. Coupling of Melt Crystallization and Distillation
Melt crystallization has been compared with traditional distillation methods. The comparison indicates that distillation is characterized by high energy consumption and high costs, making it unsuitable for separating substances with close boiling points or azeotropic systems (Sun et al., 2008). However, the mass transfer rate and phase separation rate in the melt crystallization process are relatively slow, leading to long production cycles. Additionally, the product recovery rate in melt crystallization is limited, resulting in low production efficiency. To achieve high-purity products using melt crystallization, multi-stage separation equipment is often required. By combining melt crystallization with rectification techniques, the two methods can complement each other’s shortcomings, thereby improving both purity and efficiency.
At temperatures of 250–270°C, the content of 2,6-dimethylnaphthalene (2,6-DMN) in coal tar ranges from 5% to 15%. Ban et al. (2019) enriched the 2,6-DMN content in coal tar to 11.56% through vacuum distillation, followed by melt crystallization to remove other isomeric impurities. This process ultimately produced 2,6-DMN with a purity of 62.64% and a yield of 68.12%. The introduction of distillation significantly reduced the loss of 2,6-DMN and improved product purity.Zhou et al. (2019) employed a vacuum distillation-melt crystallization coupling process, as shown in Figure 1. Vacuum distillation was used to remove most impurities from industrial-grade 1,3-propane sultone (1,3-PS), while melt crystallization eliminated impurities with boiling points similar to that of 1,3-PS. The final product achieved a purity exceeding 99.90% and a yield also exceeding 99.90%. This coupling technology not only improved production efficiency and reduced energy consumption but also enhanced key product parameters such as color and moisture content.Spielmann (2020) used distillation to remove low-boiling-point impurities from crude melts containing alkyl sulfonates collected from the top of the distillation column. The solution flowing out from the bottom of the distillation column was then purified via melt crystallization. High-purity alkyl sulfonates were subsequently obtained through solid-liquid separation and washing operations. Compared with previously employed methods, this approach exhibited lower energy consumption and offered a novel pathway for purifying various alkyl sulfonates and hydrates.Additionally, the distillation-melt crystallization coupling process plays a crucial role in extracting ultra-pure semiconductor materials. Potolokov and Fedorov (2012) removed the majority of impurities such as B, Si, Ca, Mg, and Ni from metallurgical mixtures via distillation to obtain crude tellurium and cadmium. These were further purified using melt crystallization to achieve tellurium and cadmium with a purity of 99.9999%.
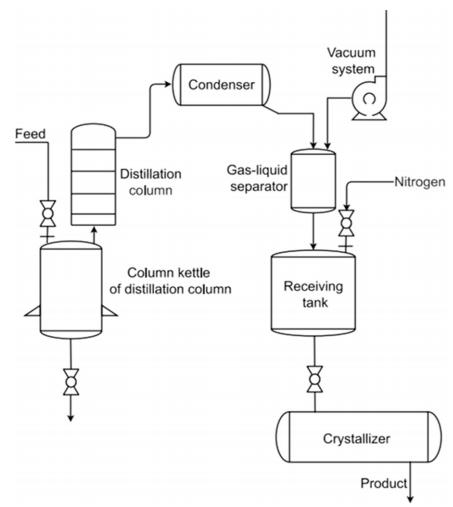
Figure 1 - Schematic Diagram of the Vacuum Distillation-Melt Crystallization Coupling System (Zhou and Wang, 2019)
The coupling of distillation technology and melt crystallization technologies for separating isomeric mixtures with similar boiling points has been widely applied. This combined process is significant in reducing energy consumption and costs, minimizing environmental pollution, and improving product purity. However, the mixed separation approach involves complex operations and multiple degrees of freedom, which are proportional to the number of components and unit operations considered. Consequently, designing processes for such challenges becomes a highly demanding task, limiting the broader application of distillation-crystallization coupling technology.Marquardt et al. (Wolfgang Marquardt, 2008) introduced a three-step approach for separating multicomponent mixtures and identifying optimal methods. Similarly, Franke et al. (2008) applied a three-step design method to develop a separation process for ternary isomeric mixtures, providing a valuable reference for cost optimization in other mixed separation processes. However, the three-step method assumes that all crystallization and cost functions are known, which is often difficult to achieve in practice.To address these limitations, Micovic et al. (2013) proposed a four-step design method. This approach overcomes the shortcomings of the three-step method and can be applied in the early stages of process development, especially when experimental data are lacking.
2. Coupling of Melt Crystallization and Extraction
The extraction method separates mixtures based on differences in solubility between substances in immiscible solvents. The extraction-crystallization process can be viewed as the result of coupling “extraction” with “crystallization.” Its principles can be divided into two categories:1. The interaction force between the extractant and the solvent is greater than that between the target product and the solvent. The combination of the extractant and the solvent reduces the solubility of the target product, which then precipitates through crystallization.2. The extractant combines with the target product through chemical bonds or other interactions, leading to crystallization and precipitation of the product.Extraction-crystallization is suitable for separating components with similar physical properties, such as volatility or boiling points, and has been widely applied in the separation of inorganic salts, organic compounds, and other materials (Qu et al., 2004).
Many researchers have achieved excellent results in the separation and purification of substances using the coupling process of melt crystallization and extraction. Hammon et al. (2006) developed a method for purifying melts in at least one monomer raw material. In this process, a crude melt of one or more monomers is obtained through extraction or other methods, and then melt crystallization is used to separate one or more monomers from the crude melt.Li et al. (2015) worked on the separation and purification of phenazine from waste generated during the production of 4-aminodiphenylamine. The process flow is shown in Figure 2. First, crude phenazine is separated from the waste liquid via melt crystallization. Next, impurities in the crude phenazine are removed using extraction. The resulting phenazine is recrystallized to obtain the final product, which has a phenazine purity of 99.5% and a yield of approximately 85%.Compared with traditional separation methods, the coupling process reduces pollution from the “three wastes” (wastewater, waste gas, and solid waste), lowers production costs, and plays a significant role in enhancing by-product value, achieving cleaner production, and promoting sustainability.
The coupling of melt crystallization and extraction processes offers advantages such as low energy consumption, short operational cycles, and minimal pollution from the extraction process. Additionally, it leverages the high separation factor of melt crystallization. This coupling simplifies the process flow and enhances separation efficiency.
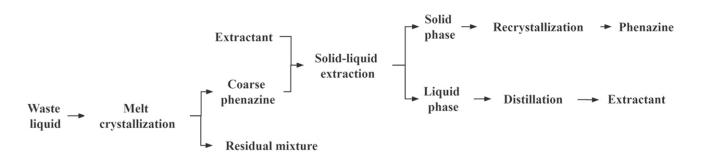
Figure 2 - Schematic Diagram of the Process for Extracting Phenazine from 4-Aminodiphenylamine Production Waste (Li et al., 2015)
3. Coupling of Melt Crystallization and Solution Crystallization
Solution crystallization is a process where solute crystallization occurs in a solvent by lowering the temperature, evaporating the solvent, or adding co-solvents to reduce the solute’s solubility and increase the solution’s supersaturation. The driving force for solution crystallization is the mass transfer process, while the driving force for melt crystallization is the heat transfer process (Zhou, 2019).When comparing the two crystallization methods, solution crystallization typically requires large amounts of solvent, which may lead to environmental issues. Although melt crystallization does not require the addition of solvents, its energy consumption is higher than that of solution crystallization. Therefore, it is worth considering combining these two crystallization methods to achieve better separation results.
Zhou et al. (2019) used a coupled melt crystallization and solution crystallization method to purify succinic acid from a mixed dicarboxylic acid solution containing succinic acid, glutaric acid, and adipic acid. First, the mixed dicarboxylic acid solution was separated by solution cooling crystallization, and the solvent was removed from the mother liquor using a rotary evaporator. After optimizing the process parameters, the content of glutaric acid was increased from 56% to 85%. After two stages of melt crystallization, glutaric acid with a purity greater than 99% was obtained. The process flow is shown in Figure 3.
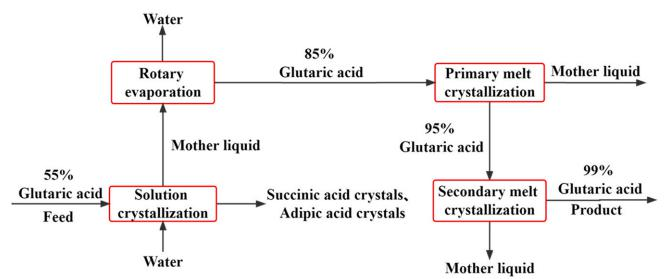
Figure 3 - Process Flow Diagram of Glutaric Acid Coupled Crystallization Purification (Zhou, 2019)
The coupling process achieved the goal of separating and purifying high-value-added glutaric acid from low-value byproducts, which has strong guidance for industrial applications.
The coupling of melt crystallization and solution crystallization can also be used to separate isomers. Cheng et al. (2022) applied this method to separate a mixture of dimethyl phthalate (DMO), iso-dimethyl phthalate (DMI), and terephthalic acid dimethyl ester (DMT). The mixture was first separated by cooling crystallization and solid-liquid separation, resulting in two phases. The solid phase, which contained almost no DMO, was subjected to two continuous melt crystallization stages to yield DMT and DMI products with purities greater than 99.9%. For the DMO-rich liquid phase, after solvent evaporation, a small amount of DMT and DMI impurities precipitated and were separated by cooling crystallization, resulting in a DMO product with purity greater than 99.0%. This process achieved solid residue recovery and high-purity products under low-energy consumption conditions.Ban et al. (2019) enriched 2,6-dimethylnaphthalene (2,6-DMN) through vacuum distillation, obtaining a solution with a dimethylnaphthalene isomer content greater than 90%, while the content of 2,6-DMN was only 30.9%. Based on the melting point differences of these isomers, the solution was separated through melt crystallization to obtain 2,6-DMN with a purity of 62.4% and a yield of 68.12%. The product was then subjected to solution crystallization. By optimizing conditions such as cooling rate and crystallization temperature, it was found that increasing the cooling rate lowered both product purity and yield. While reducing the crystallization temperature improved the yield, the purity also decreased accordingly. After adjusting the test parameters and performing three stages of solution crystallization, the final purity of 2,6-DMN reached 99.7%. This process achieved the purification of 2,6-DMN from coal tar through the coupling of melt crystallization and solution crystallization.
4. Coupling of Melt Crystallization and Membrane Separation
In recent years, membrane separation technology has developed rapidly due to its advantages such as simple operation, high selectivity, low pollution, and low energy consumption, attracting increasing attention. A membrane is a material with selective permeability, allowing only one or a few substances to pass through, while different substances pass through the membrane at different rates. Membrane separation technology is driven by performance differences (such as pressure, concentration, etc.) across the membrane, using its selective permeability to achieve separation. It has wide applications in the separation and purification of drinking water or wastewater, production of fine chemicals, and biopharmaceuticals (Baker, 2010).However, membrane separation technology has its drawbacks, such as poor acid and alkali resistance, low mechanical strength, and poor high-temperature resistance (Liu et al., 2021). Therefore, coupling membrane separation technology with melt crystallization can be applied in industrial production processes to achieve better separation results.
Ling et al. (2022) used a multi-step melt crystallization process to treat industrial EDTA-2Na, then dissolved the melt crystallization product in high-purity water and filtered it through a microporous membrane. The water in the filtrate was evaporated, and the concentrated solution was crystallized to obtain a product that met the standards. This coupled process addressed the issue of low metal ion content in EDTA-2Na, significantly improving its quality.Xie et al. (2022) employed steam distillation to remove naphthalene from crude ortho-cresol, followed by the addition of sodium bicarbonate to neutralize the organic phase. The solution was filtered using a metal membrane under stirring conditions to remove valeric acid and prevent corrosion in the system. The neutralized organic phase was treated three times to obtain phenol, ortho-cresol, and meta/para-cresol. Since the obtained ortho-cresol contained a small amount of 2,6-dimethylphenol, it was purified by melt crystallization. Finally, after decolorization, ortho-cresol with a purity higher than 99.5% was obtained. The entire process flow is shown in Figure 4.Kontos et al. (2018) used membrane separation technology to separate phenolic substances from wastewater containing a large amount of high-value products from an olive processing plant. The solvent was then removed by vacuum evaporation, cooling, and drying to further purify the phenolic substances. Finally, melt crystallization was used to obtain a product with high purity. Compared to alternative processes such as evaporative crystallization, this method can operate at lower temperatures, effectively avoiding the evaporation of phenolic compounds.
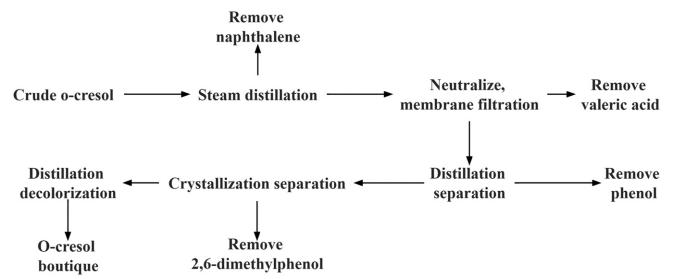
Figure 4 - Process Flow Diagram for Purification of Ortho-Cresol (Xie et al., 2022)
Conclusion
The coupling of melt crystallization with other separation technologies offers significant advantages in low-carbon, energy-saving, and green production. It can save energy, reduce carbon emissions, and is suitable for separation and purification needs across various industrial fields. With the increasing demand for sustainability and green practices, such coupling technologies for ultrapure separation are expected to see broader application and promotion in the industry. This will help reduce energy consumption in chemical separation processes and contribute to achieving the national “dual carbon” goals, creating a low-carbon, high-end industrial future.
References
Sun, S., et al., 2008. Process development of melting crystal- lization. Chem. Eng. (China) 36 (12), 18–20+24.
Ban, H., et al., 2019. Preparation of high-purity 2,6-naphthalene-dicarboxylic acid from coal tar distillate. Chem. Eng. Technol.42 (6), 1188–1198.
Zhou, J., Wang, B., 2019. Study on separation of 1,3-propane sultone by vacuum distillation and melt crystallization. Guangzhou Chem. Ind. 47 (06), 76–77.
Spielmann,J.M., DE), Koch, Michael (Speyer, DE), Wortmann,Juergen (Limburgerhof, DE), Ruether, Feelly (Frankenthal, DE), Weiguny, Sabine (Freinsheim, DE), Borgmeier, Frieder
(Mannheim, DE), Process for purifying alkanesulfonic acids. 2020, BASF SE (Ludwigshafen am Rhein, DE): United States.
Potolokov, N.A., Fedorov, V.A., 2012. Ultrapurification of tellurium and cadmium by distillation and crystallization. Inorg. Mater. 48 (11), 1082–1087.
Wolfgang Marquardt, S.K., Kraemer, Korbinian, 2008. A frame-work for the systematic design of hybrid sparation processes Chin. J. Chem. Eng. 16 (3), 333–342.
Franke, M.B., et al., 2008. Design and optimization of a hybrid distillation/melt crystallization process. AICHE J. 54 (11),2925–2942.
Micovic, J., et al., 2013. Design of hybrid distillation/melt crys-tallisation processes for separation of close boiling mixtures.Chem. Eng. Process. -Process. Intensif. 67, 16–24.
Qu, H., et al., 2004. Research progress on extractive crystallization process. Chem. Propellants Polym. Mater. 05, 26–29.
Hammon, U.M., DE), Eck, Bernd (Viernheim, DE), Baumann, Dieter (Walldorf, DE), Heilek, Joerg (Bammental, DE), Mueller-engel, Klaus Joachim (Stutensee Blankenlock, DE), Method for the production of a purified melt of at least one monomer. 2006, BASF Aktiengesellschaft (Ludwigshafen, DE): United States.
Li, M., et al., 2015. Study on Extract Phenazine by Use of Waste from the production of 4-amino Diphenylamine Shandong Chemical Industry 44 (05), 10–11+15.
Cheng, Y., et al., A kind of crystallization separation method of dimethyl phthalate mixture.
Zhou, Y., 2019. Purification of Glutaric Acid by Solution Crystallization-Melt Crystallization Hybrid Separation Process. Hebei University of Technology.
Xie, F., et al., A Kind of Purification Method of O-Cresol.
Baker, R.W., 2010. Research needs in the membrane separation industry: Looking back, looking forward. J. Membr. Sci. 362(1–2), 134–136.
Liu, J., et al., 2021. Research progress on membrane separation technology. Guangzhou Chem. Ind. 49 (13), 27–29+71.
Ling, F., et al., A Kind of Method for Improving the Quality of Industrial EDTA-2Na.
Kontos, S.S., et al., 2018. Implementation of membrane filtration and melt crystallization for the effective treatment and va-lorization of olive mill wastewaters. Sep. Purif. Technol. 193, 103–111.